3Dプリンティング技術導入支援
- ホーム /
- サービス・ソリューション /
- 3Dプリンティング技術導入支援 /
- 導入事例 /
- ジヤトコ株式会社
解析×設計×3Dプリンターにより、マシニングセンターの切子詰まり防止ノズル製作に協力 ~チョコ停・故障を減らし、生産効率を向上~
自動車部品メーカー
ジヤトコ株式会社
ジヤトコ株式会社について
ジヤトコ株式会社は、自動車用オートマチックトランスミッションの専門メーカーとして自動車用変速機、電動パワートレインおよび部品の開発・製造・販売を行っています。ステップATや環境に優しいCVT、ハイブリッド車用のトランスミッションなど幅広い商品を生産しています。
3Dプリンターの活用により生産ラインを効率化
ジヤトコ様は1つの部品の生産に、10台ものマシニングセンターを使用しています。しかし、マシニングセンターでの加工時、大量の切子が堆積することにより設備が一時停止したり、加工中の部品を傷つけてしまったり、設備の隙間に挟まり故障を引き起こしたりしていました。
その課題を解決すべく、社内にある3Dプリンターを活用して、切子を洗い流すためのノズルを製作しました。しかし、狙った箇所にクーラントを到達させることは至難の業でした。狙った箇所にクーラントを到達させるため、解析技術を用いたノズルの設計と3Dプリンターによるノズル製作をSOLIZEに依頼しました。
モデル作成と解析には膨大な時間が必要となりますが、予算と要望に合わせた必要最小限の解析にすることで解析時間を1/10に抑え、その分、複数パターンのノズル形状の検討に時間を割きました。3Dプリンターだからこその自由な設計と適切な流体解析をうまく組み合わせることで、クーラントを均一に狙った位置に噴射するノズルをわずか2週間で設計しました。当初の想定よりも広い範囲にクーラントを噴射できるノズルの製作に成功し、生産ラインの効率化に寄与しました。
Before
導入前の課題
- 電動化シフトが急ピッチで進む中、競争力強化のため生産効率を向上させる必要がある。
- マシニングセンターでの加工時、大量の切子が堆積してしまい、設備の一時停止や、製品へのダメージ、設備の故障を招き、生産効率が悪化していた。
- マシニングセンターにはクーラントを天井に噴射する機能がなく、自作のノズルを製作したが、狙った位置にクーラントを噴射することができなかった。
After
導入後の効果
- 切子による不具合を発生させず、清掃作業も削減できた。
- 必要最小限の情報で的確な解析を実施し、時間とコストを削減できた。
- 3Dプリンターの活用により、短期間で製作することができた。
- 最新3Dプリンターの活用により、ノズル自体に切子を堆積させない、丸くつるっとした滑らかな表面を実現した。クーラント噴射のため内部流路に突起を設けるなど、解析結果を反映した複雑形状を難なく再現できた。
解析×設計×3Dプリンターを活用したノズル設計
Step1.ヒアリング
- お客さまの困りごとに対し、事象を確認して対策を整合
マシニングセンター内の切子除去のため、お客さまが社内で製作したノズルでは上部シャッターにクーラントが届かず、切子除去ができませんでした。上部シャッターかつ広範囲に届くノズル設計が必要でした。 - 対策の効果を確認できる解析方法の提示
設計を進めるにあたり、ノズル内部とノズルから噴射した後の流体解析をすべて行う場合、膨大な工数がかかります。そのため、上部シャッターにクーラントが届くノズルの設計には、ノズルから噴射した後の詳細な解析は不要と判断し、理論値の計算で求める手法に変更しました。コストを抑え、短期間で設計変更の効果を確認できる手法を提案しました。
Step2.吹き流しノズル吐出高さを検討し、目標高さを設定して目標点に到達する吐出圧(動圧)を満たす出口形状を作成
- 解析を迅速に行うために、的確な目標値を設定
解析を行ううえで、現状のノズルに対して相対的な比較ができる値を設定しました。現状のノズルの吐出高さから、目標高さまでの差分を算出し、流体解析で求める数値を決定しました。既存のノズルでは、中心の出口から目標点まで1.5倍、左右の出口からは2倍の吐出高さが必要です。 - 目標高さに到達するノズル出口幅を算出
現状のノズルの動圧を解析し、目標高さに到達させられる必要動圧を検討しました。解析の結果、現状の出口幅8mmに対して真ん中を6.5mm、両端を5.5mmにすることで、目標とする動圧が確保できることがわかりました。
Step3.吹き流しノズル範囲の検討
Step3-1.現状のノズルに対して広がり角を設定した際のノズルを検討
- 3口ノズルの吹き流しノズル範囲検討
現状のノズルでは目標高さに到達してもクーラントが届いて欲しい範囲まで広がらないため、ノズルの角度を調整してクーラントが行き届くようにしました。マシニングセンター庫内に3口ノズルを1本設置するだけではクーラントが届かないので、3口ノズルが2本の場合、3本の場合にカバーできる範囲を算出しました。今回は庫内に2本使用のため、だいだい色の範囲となります。
Step3-2.最適なノズル個数での新形状を追加提案
- 新形状の10口ノズルを考案
3口ノズルでの最適化設計に加えて、新形状を検討しました。ノズルの口数を増やすことで、広範囲にクーラント噴出できるようになるため、目標吐出範囲に対し、最適なノズルの数を決定しました。 - 3Dプリンターでの製作を見据えた設計
ノズル出口が細い方が天井までしっかり届くのですが、細すぎるとクーラントが出づらく、造形もしづらいので、細すぎない最適なノズル径を設定しました。天井まで届かせるために必要な動圧から、形状を策定しました。 - 均一かつ広範囲に噴出するように設計
吹き出し口の個数検討に加え、個数を増やした際に吹き出し口から均等にクーラントが噴出するように、内部に圧力を分散させる構造を追加し、設計変更しました。 - ノズルの外形に設計の工夫
マシニングセンター庫内でノズル本体にごみがたまらないよう、ノズルの外側をなめらかな形状にしました。
Step4.吹き流しノズルを3Dプリンターの透明材料で製作
流路を観察できるよう透明材料を用いて、今回設計した2種類のノズルを3Dプリンターで製作しました。
- 製作方法:Figure 4(吊り下げ式光造形機)
- 材料:Tough Clear
- 仕上げ:サポート除去、クリア塗装
ノズル製作に使用した透明材料を含む、Figure 4の無料サンプルを提供しています。
インタビュー:3Dプリンターを活用した生産性向上の取り組み
ジヤトコ株式会社
部品技術部 第一加工技術課
課長
曽和 真弘様
生産性向上に向けて、マシニングセンターでの切子トラブル改善の取り組みを開始。
Q.マシニングセンターでの切子の課題について詳しく教えてください。
弊社は長年にわたり、ステップATやCVTのトランスミッションを製造してきました。しかし近年、自動車業界は電動化にシフトしており、弊社も電動化に大きく舵を切っているところです。電動化に伴い、今まで以上にコスト競争力を求められるようになりました。私が担当しているアルミ部品の加工ラインは、いかに生産性を向上させコストダウンできるかが使命になっています。
生産ラインではマシニングセンターを使用して部品を製造しているのですが、マシニングセンター内で大量に発生する切子が詰まってしまったり、機械の駆動部分にくっついてしまって製品ダメージを起こしたり、設備が故障したり停止したりするため、生産性を悪化させていました。生産性を向上させるためには、切子によるトラブルをいかになくせるかが大きな課題でした。クーラントを使用しているので、それをいかにうまく活用して切子を流せるかが今回の活動のポイントでした。
Q.これまで切子によるトラブルにはどのような対策をしていたのでしょうか。
おもな対策としては、掃除を定期的に行うことでした。週に2回、月に2回などになるのですが、生産が忙しい時には掃除の時間が確保できないこともあり、そうするとある日突然、設備が故障してしまい、結果的に何日も生産が停止してしまうことが多々ありました。
Q.切子によるトラブルにより、どのようなロスが発生していたのでしょうか。
マシニングセンターの駆動部分に切子が堆積することによる設備故障のロスと、加工対象の部品を自動で固定するためクランプする際に切子を巻き込んでしまうことにより、アラームが出てラインが止まってしまう「チョコ停」によるロス、そしてその切子を取り除くために、人の手で掃除を行うロスが発生していました。ほかにもあると思いますが、その辺りがおもなロスになっています。
解析技術を持ち合わせるSOLIZEに相談。提案型で設計をリードしてくれた。
Q.ノズルを3Dプリンターで製作しようと考えたきっかけをお聞かせください。
3Dプリンターが一般的になってきた中で、3Dプリンターをいかに生産ラインで活用できるかを考えていました。社内に3Dプリンターを導入し、手軽に活用できる環境が整備されています。おもな使い道は設備設計検討用のモック製作で、加工治具などに使えないかと、いろいろと挑戦していました。
その中で複雑形状が作れることを実感し、ノズルを製作したらおもしろいのではないかと考え、課題になっていた切子を洗い流すためのノズルを製作してみたのですが、まったくうまくいきませんでした。思うようにクーラントが飛ばない状況でした。
別のモックアップ製作の件でお話していたSOLIZEさんとの会話の中で、SOLIZEさんは解析技術も持っていると伺い、私たちのニーズとSOLIZEさんの強みがマッチしたので、ノズル製作を依頼することになりました。
Q.SOLIZEの解析や設計提案はいかがでしたか。
私たちは解析にあまり詳しくないため、設備のこういうところにつけたい、どのくらいクーラントを飛ばしたい、極力広い範囲に飛ばしたい、何リッターくらいのクーラントがきます、というような情報しかインプットできなかったのですが、そこからSOLIZEさんがいろいろと提案してくれたので非常に嬉しかったです。
当初の想定では、口を平たくすれば遠くまで飛ぶのではないかと思っていました。しかしSOLIZEさんは、ノズルの口の形は長穴より小さな丸穴、3口より10口の方がよいと、提案してくれました。解析を回しながらもっとこういう形の方がよいと、提案型で設計を進めていただけたのがありがたかったです。特に弊社は知見がないところでしたので助かりました。
Q.初回の打ち合わせから解析・設計をして3Dプリンター品を納品するまで3週間ほどでした。スピード感はいかがでしたか。
むしろ私たちがついていけないほどのスピード感で、逆にフォローしていただいたくらいでした。
社内の3Dプリンターではできない滑らかな表面と小さいノズル口をきれいに再現
Q.今回、Figure 4という最新の吊り下げ式光造形機を活用してノズルを製作しました。完成品の感想をお聞かせください。
今回納品してもらったものは、表面がなめらかで、丸みを帯びた形状でした。そもそもノズル自体に切子が付いてしまってはいけないので、ノズル自体に切子が付きにくい、付いたとしても流れ落ちやすい形状・表面になっているので、とてもよいです。弊社にはノズルから押し出すタイプの3Dプリンター(材料押出/熱溶解積層法)しかないため、社内の3Dプリンターでは積層が表面に残るので難しいだろうと思いますし、ノズルの先端の穴もこれほどきれいにならないと思います。また、特に透明だから値段が高いということもなく、透明にしたことで何か不具合があった時に中が詰まっているなどがわかるので、その点もよかったです。
Q.今回初めての取り組みということでしたが、社内の反応はいかがでしたか。
社内の反応はとてもよいです。現在、eアクスル向けのラインを立ち上げており、その設備に今回製作したノズルを入れています。新しいラインの立ち上げということで、役員が現場の確認に来ることもあるのですが、その際に「切子の課題が多々あったので、新しい取り組みとして、ノズルを付けて対策しようと思っています」と紹介しています。最新の技術をうまく融合させてよい取り組みができている、と評価いただき、よい反応をもらえています。
Q.今後の3Dプリンター活用の展望をお聞かせください。
今回製作したノズルをすべてのマシニングセンターに展開していきたいので、SOLIZEさんに発注しようと思っています。今後の3Dプリンターの活用については、より活かせるものがあると思ってはいるのですが、まだアイデアが足りない状況です。搬送用パレットの治具などいろいろ試しているのですが、さらに挑戦していきたいと思っています。
- ※所属部署・役職は本活動推進時のものです
滑らかな表面と小さいノズル口をきれいに再現した、Figure 4の無料サンプルを提供しています。
3Dプリンティング技術導入支援に関するお問い合わせ
サービスに関する情報をはじめとした各種資料(PDF)をご提供しています。
資料はまとめてダウンロードできます。お気軽にご利用ください。
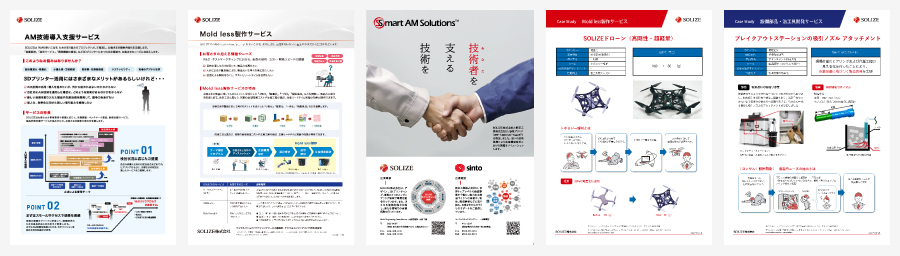
-
お電話でのお問い合わせ
受付時間 10:00-12:00、
13:00-17:00(平日のみ) -
フォームでのお問い合わせ
お見積り・お問い合わせに関する回答は、1営業日以内にご連絡します。